OUR MISSION
Supporting teams through today's challenges
Let us help you find new, better ways to manufacture parts, save costs, reach sustainability goals, and improve part performance.
From exploring new applications to demonstrating and proving parts, our team integrates with yours to advance your goals.
You know your parts, structures and challenges. We know how to help you apply advanced composites solutions, improve production rates, and lower per-part costs.
From meeting production goals to improving sustainability, you face big challenges ahead. our team can help you chart the path forward to solutions that lower costs, improve rates, and drive sustainability.
01/08
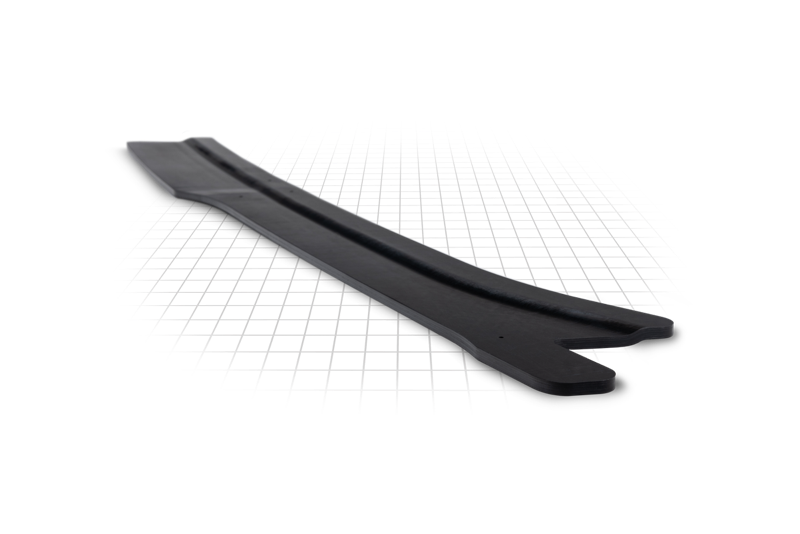
Control Surfaces & Moveables
Components of flight control systems such as ailerons, elevators, rudders, flaps and slats. TPC’s offer excellent resistance to moisture, chemicals, which enhances the longevity and reliability of control surfaces and moveables.
Learn More
Commercial Aerospace Applications
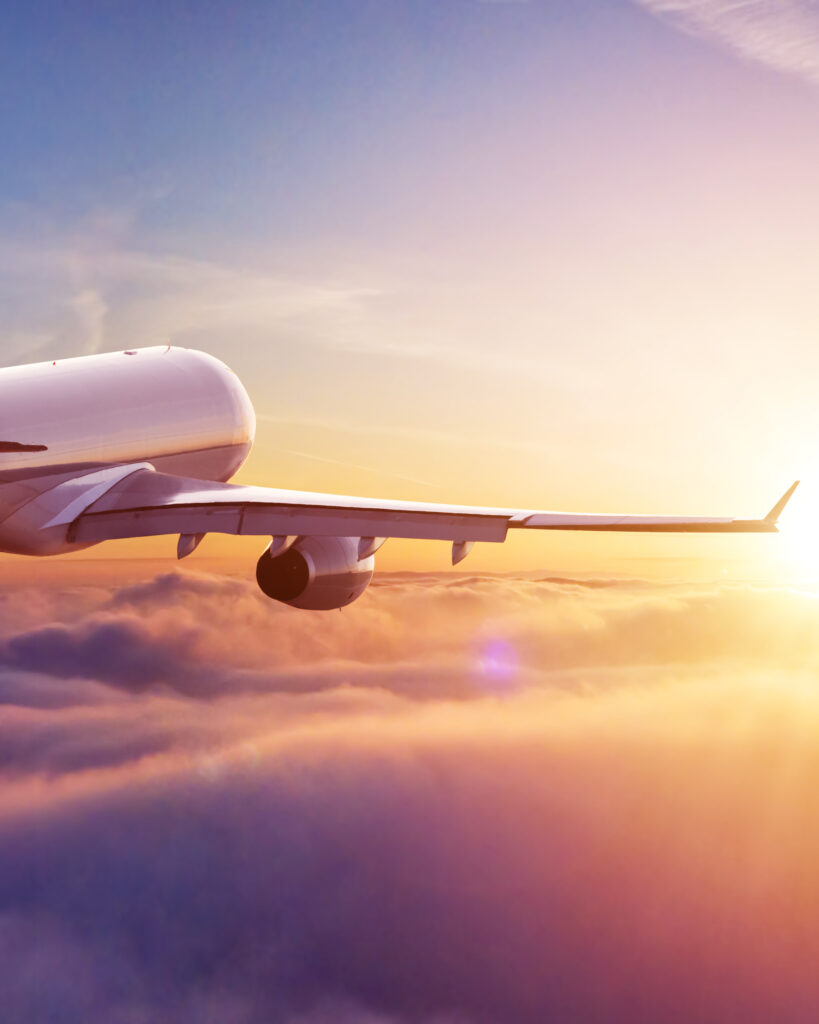
Over 2,000,000 parts flying and counting
By incorporating thermoplastic composites into aircraft design, manufacturers can achieve a balance of performance, durability, and cost-efficiency, making these materials a compelling choice for both secondary and primary aircraft structures over thermosets and metals.
These materials provide significant weight savings compared to traditional metals, contributing to improved fuel efficiency and reduced emissions. Additionally, thermoplastic composites exhibit superior impact resistance and damage tolerance, enhancing the safety and longevity of aircraft components. Their ability to be reshaped and reformed with heat allows for easier repairs and maintenance, reducing downtime and operational costs.
Manufacturing processes for thermoplastic composites are generally faster and more cost-effective than those for thermoset composites, as they do not require lengthy curing times. This results in increased production rates and lower overall costs.
ATC has produced over 2,000,000 thermoplastic composite parts for commercial aircraft currently.
Defense Applications
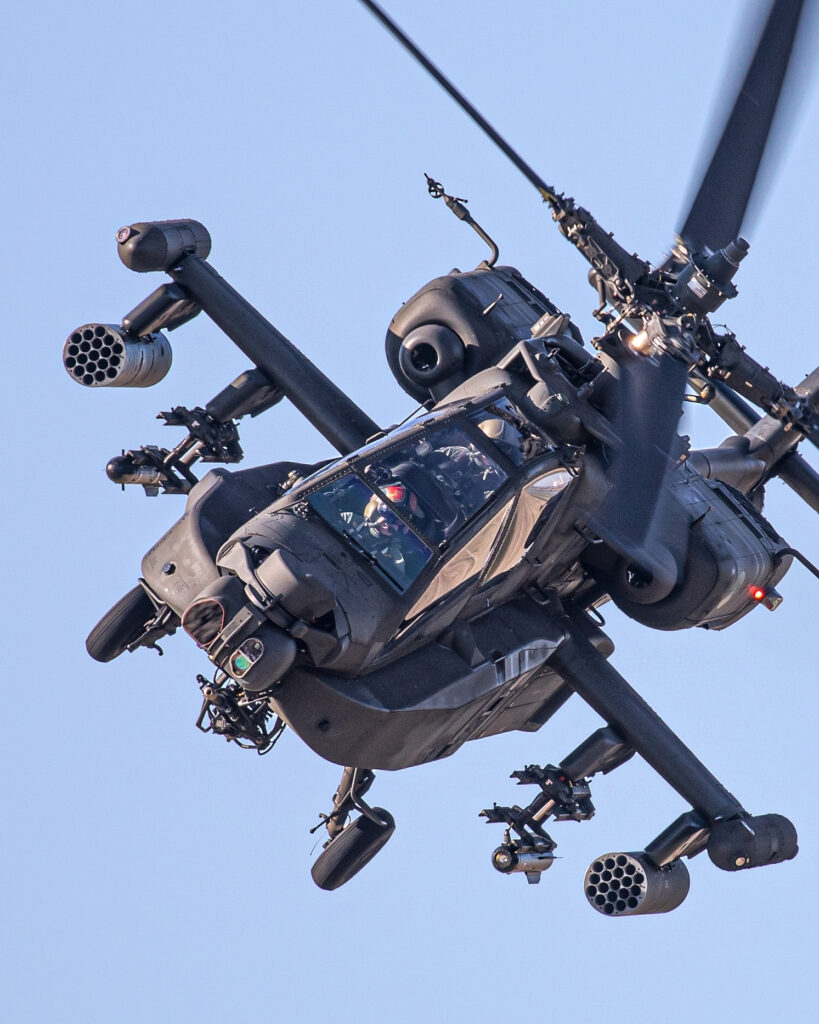
Revolutionizing Defense Aircraft with Thermoplastics
Thermoplastic composites are widely used in defense aircraft, including helicopters and airplanes, due to their exceptional properties. Thermoplastic composites offer durability, efficiency, and compliance with regulatory standards.
Common applications:
- Fuselage sections
- Wings/blades
- Tail assemblies
- Internal brackets
- Landing gear doors and weapon bay doors.
Key Benefits:
- High Strength-to-Weight Ratio: Enhances aircraft performance, increases payload capacity, and improves fuel efficiency.
- Impact and Damage Resistance: Ensures longer service life and reduced maintenance.
- Efficient Manufacturing: Allows rapid, automated production in secure, ITAR-compliant facilities.
- Thermoformable and Weldable: Reduces production cycle times and costs.
- Recyclability: Supports sustainability and easier disposal or reprocessing.
Drones & UAV's
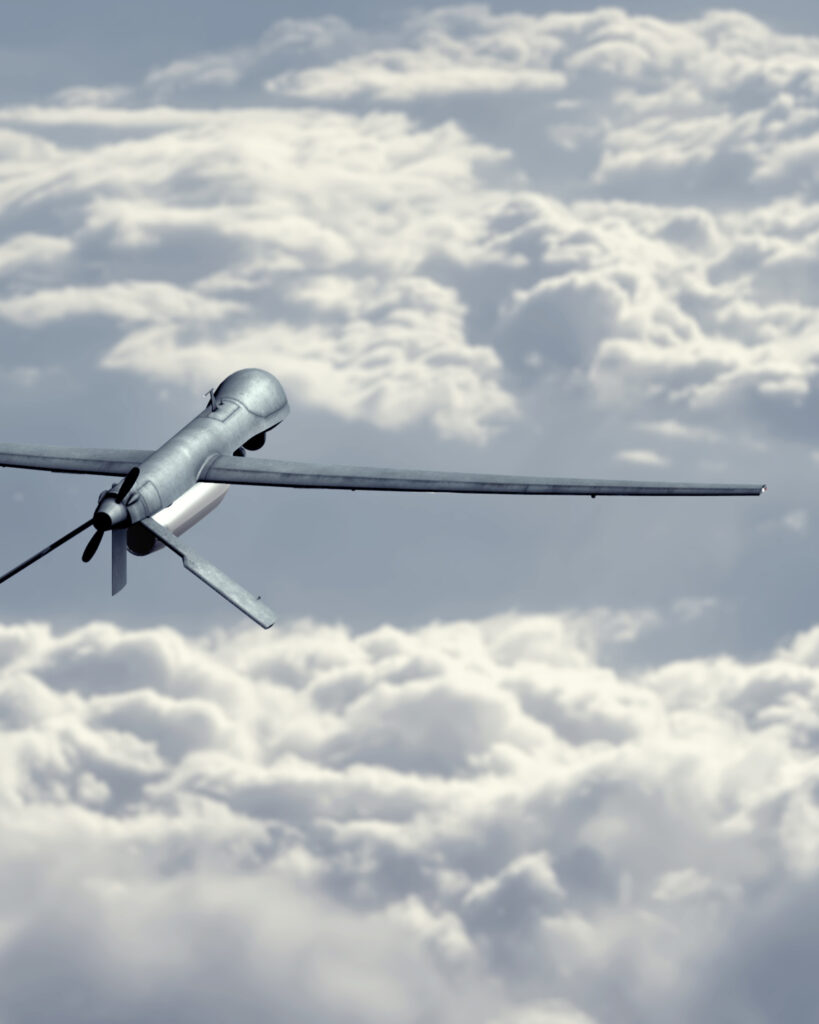
Enabling the Future
Thermoplastic composites (TPCs) are extensively used in UAVs (Unmanned Aerial Vehicles) and UAMs (Urban Air Mobility) due to their exceptional properties and benefits.
Common Parts:
- Airframes: Lightweight and strong structures.
- Propeller Blades: Durable and impact-resistant.
- Landing Gear: High strength and flexibility.
- Battery Housings: Lightweight and heat-resistant.
- Wing Components: Superior aerodynamic performance.
Key Benefits:
- Lightweight: Increases flight efficiency and endurance.
- Durability: Enhanced impact and fatigue resistance.
- Production Efficiency: TPC’s can support the high production rates for these vehicles.
- Cost-Effective: Lower production and maintenance costs.
- Sustainability: Recyclable materials support environmental goals.
TPCs offer UAV and UAM manufacturers enhanced performance, durability, and cost-efficiency, making them ideal for advanced drone applications.
Space Applications
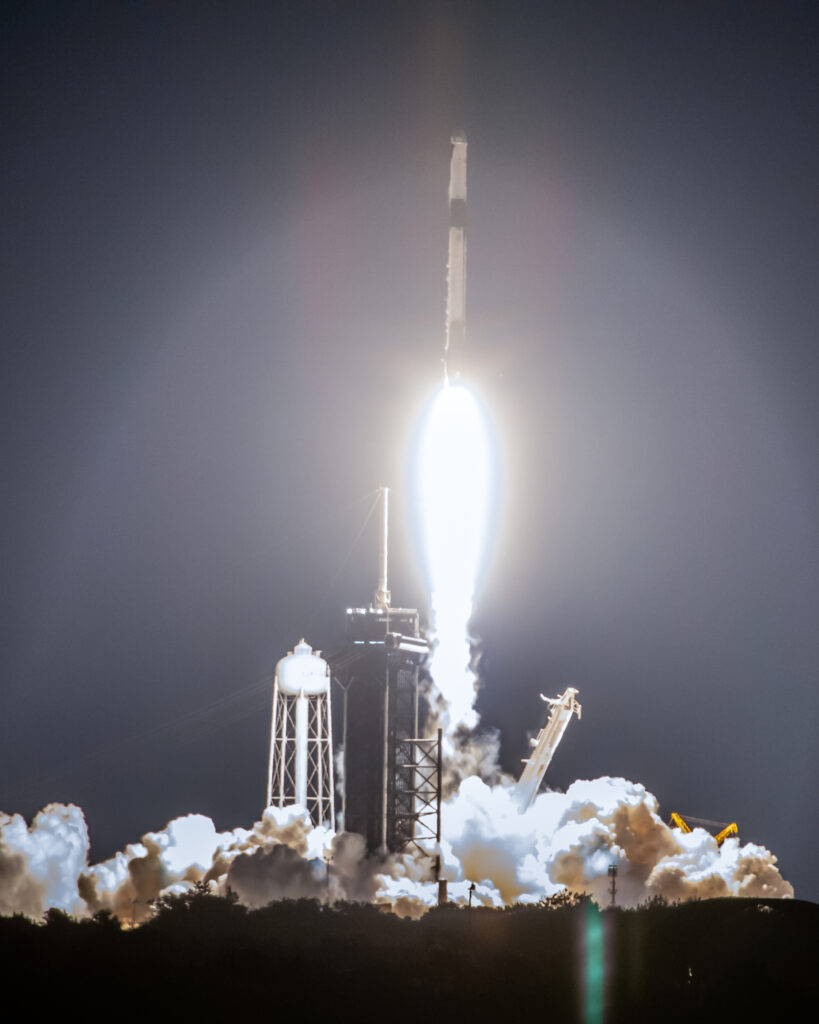
Transforming Space Structures
Thermoplastic composites are increasingly used in various space applications due to their unique properties like hygrothermal stability. Common uses include:
- Satellite Structures: Lightweight and durable panels and frames.
- Antennas and Reflectors: High strength and stability under thermal stress.
- Launch vehicles
- Spacecraft Components: Structural elements and support brackets.
These applications benefit from the material’s high strength-to-weight ratio, resistance to extreme temperatures, cryogenic properties and the ability to withstand the harsh conditions of space.
Updates & News
Celebrating 20 Years of ATC Manufacturing
ATC Manufacturing Celebrates 20 Years as a Leading Producer of Thermoplastic Composite Parts This summer, ATC Manufacturing celebrated 20 years as a leading thermoplastic composites...
Read MoreATC Earns CompositesWorld 2024 “Top Shop” Distinction
We are excited to announce that CompositesWorld has recognized ATC Manufacturing as a 2024 “Top Shop.” Prior to 2024, we have been recognized as a...
Read MoreSenators Crapo & Risch Protect Idaho Manufacturing
Idaho is fortunate to have Senators Risch and Crapo representing us in the U.S. Senate. As our country faces unprecedented challenges, meeting market demands with local manufacturing growth...
Read MoreGranting Carrigan’s Make-A-Wish
We’re delighted to share our recent experience with Carrigan through the Make-A-Wish program, marking ATC’s first time making a wish a reality. Carrigan’s Story Carrigan...
Read More